April 2024
I had the incredible opportunity to attend the 2024 SPESA Advancements in Manufacturing and Technologies Conference which took place April 11th, 2024 in Los Angeles. This was my second SPESA conference, and it exceeded my expectations for education and networking with the textile and sewn products industry. I found there to be many exciting aspects of the Los Angeles fashion industry which were inspiring to see in person for the first time in my career, and compare with Chicago, New York, and other areas of the country I have visited. The speakers and topics were very relevant and forward thinking, and meeting people in various areas of the industry was extremely valuable.
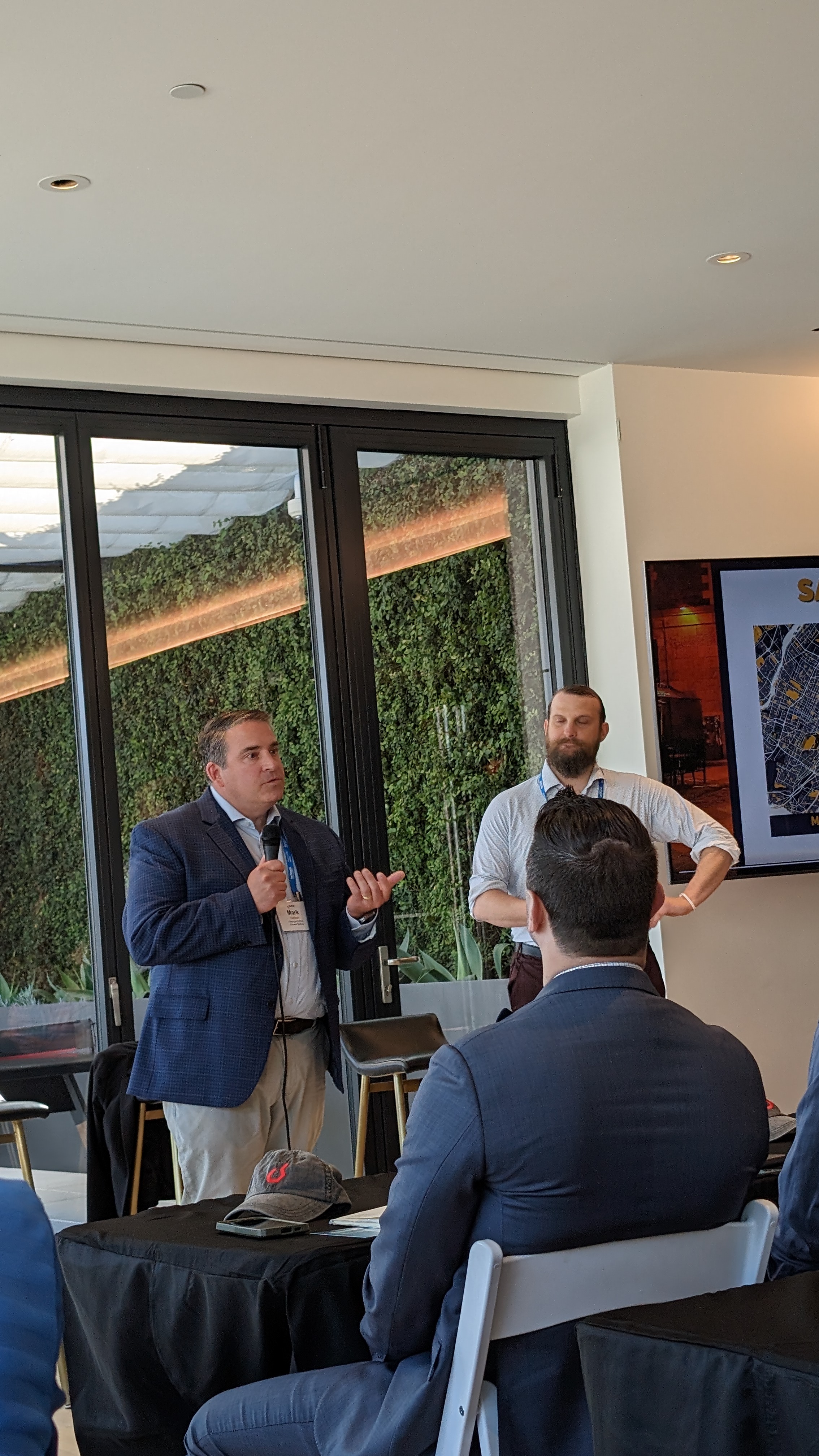
The conference opened with introductions from SPESA’s President, Michael McDonald, and Chairman Mark Hatton (American & Efird), and immediately went into the first panel which was a conversation with the Garment Worker Center in LA. Panelists represented the organization, as well as a factory owner, and a member of the City Council. They discussed the task force which was created in order to support keeping the garment district in tact, supporting workers and factories to transform “sweatshops” of the past into viable, sustainable and ethically run businesses, attract and retain skilled labor, workforce development and advocacy, and support factories as they upgraded facilities and technologies in order to comply with new regulations for safety, licensing, and to make the facilities more modern and efficient.
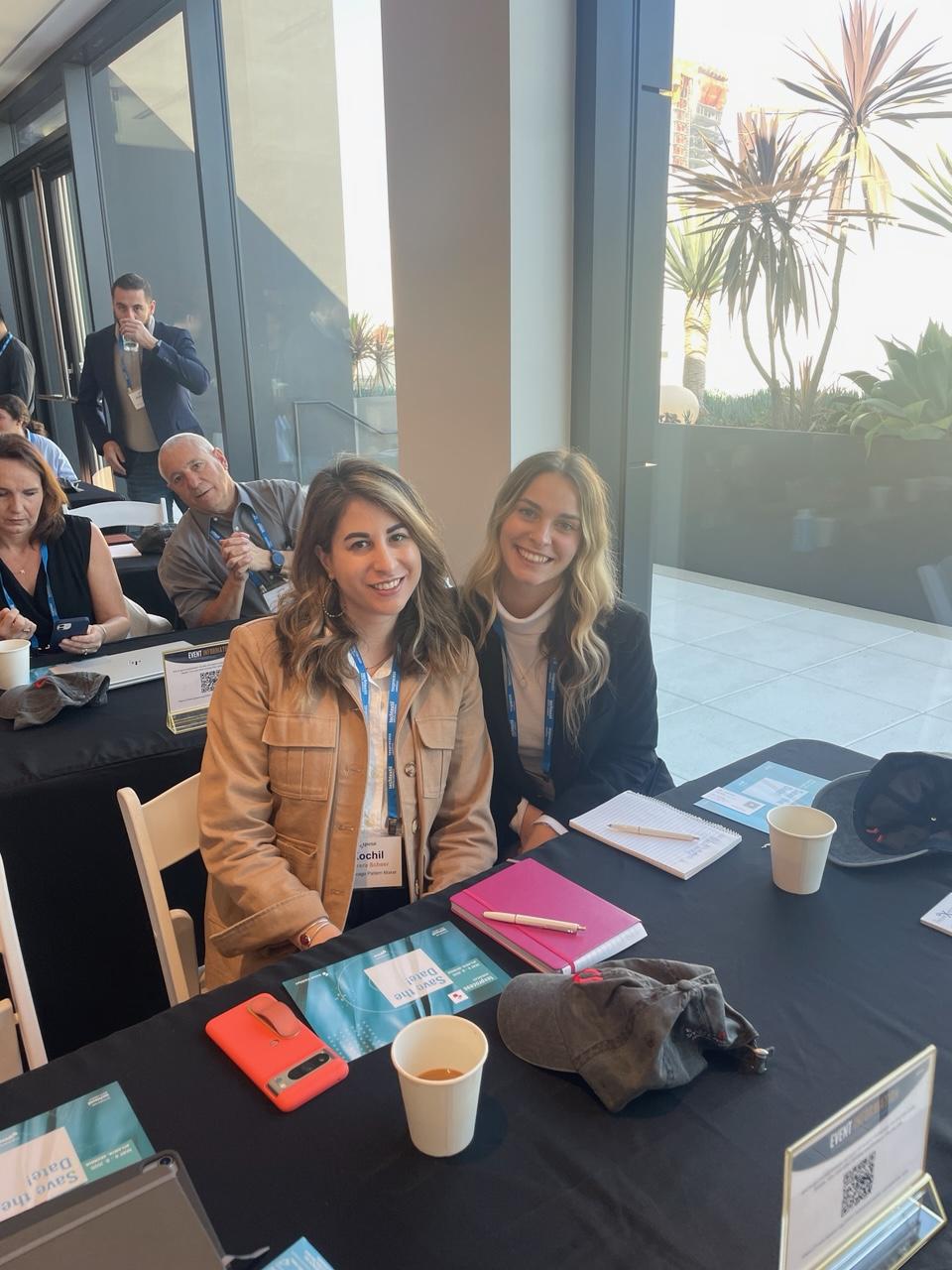
In pretty much every industry conference or conversation, workforce, or lack thereof, always comes up. Interestingly, in LA there doesn’t seem to be a lack of a willing and able workforce, however, businesses do need help in order to provide better environments, afford benefits and pay competitive salaries. Infrastructure is a consideration in making sure those workers can safely get to and from work. LA boasts 30,000 garment workers who produce approximately 835 of the nation’s $2 billion cut-and-sew apparel sales (as of 2019). Even with that, LA has more workers than work available. More production opportunities are desperately wanted.
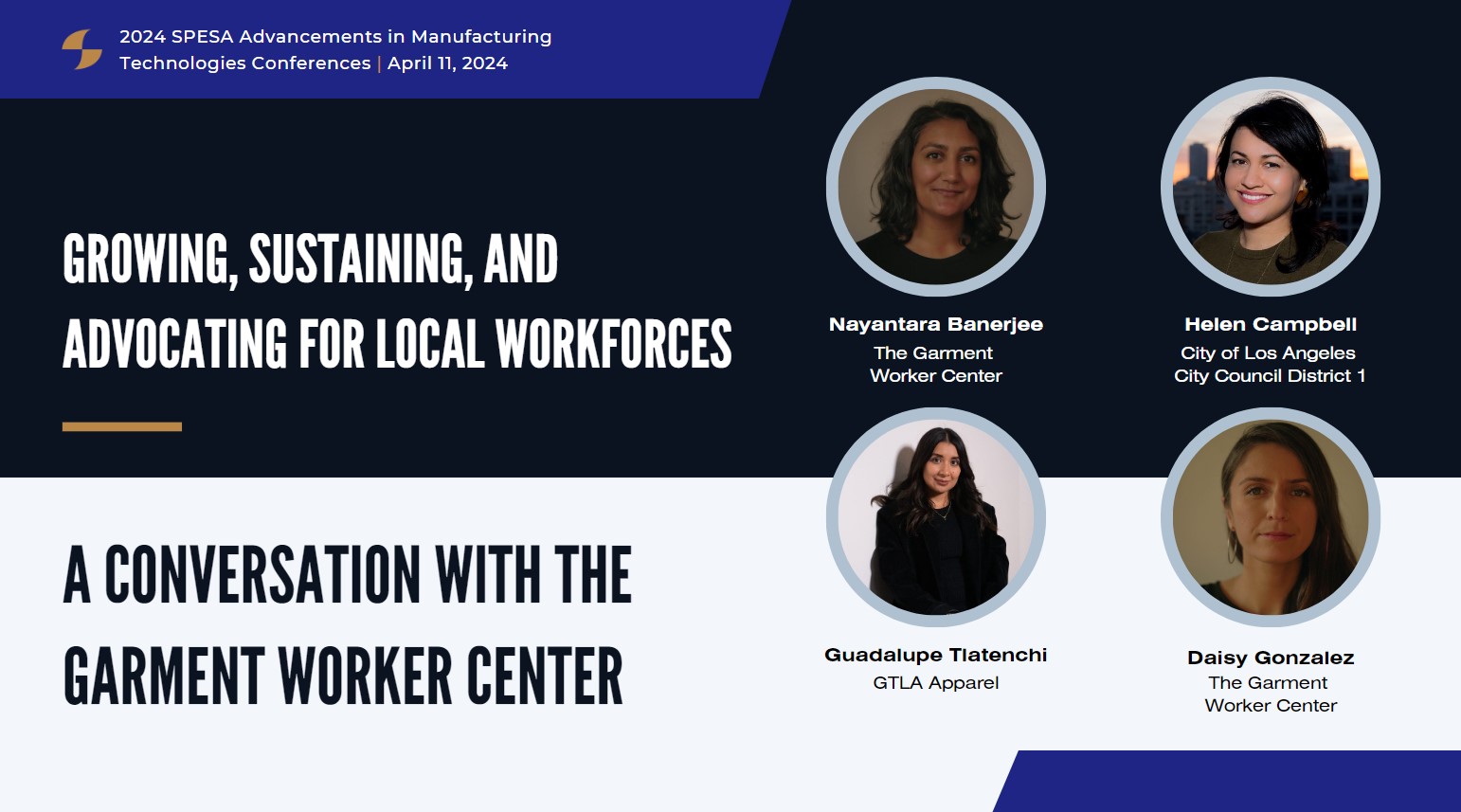
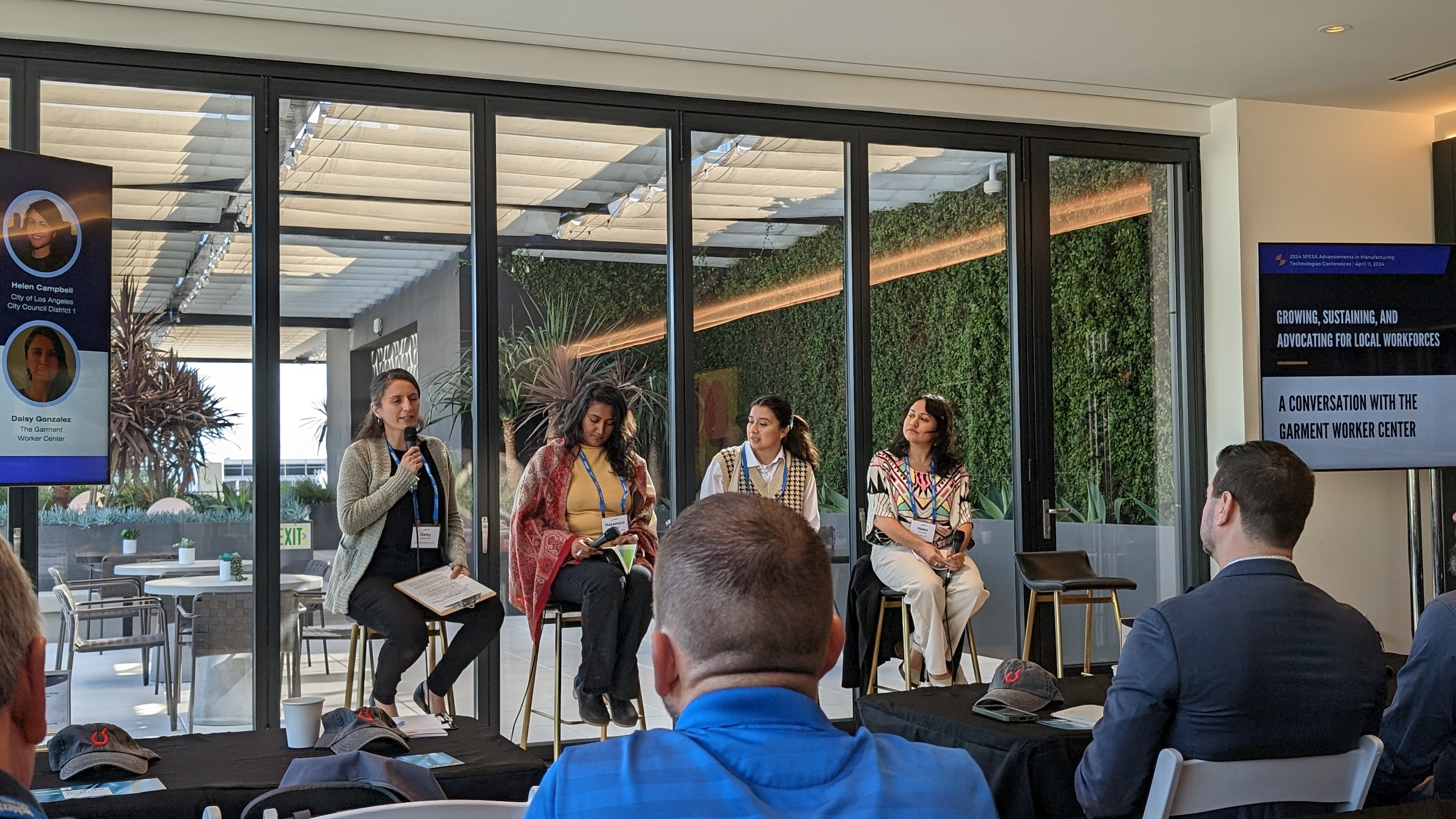
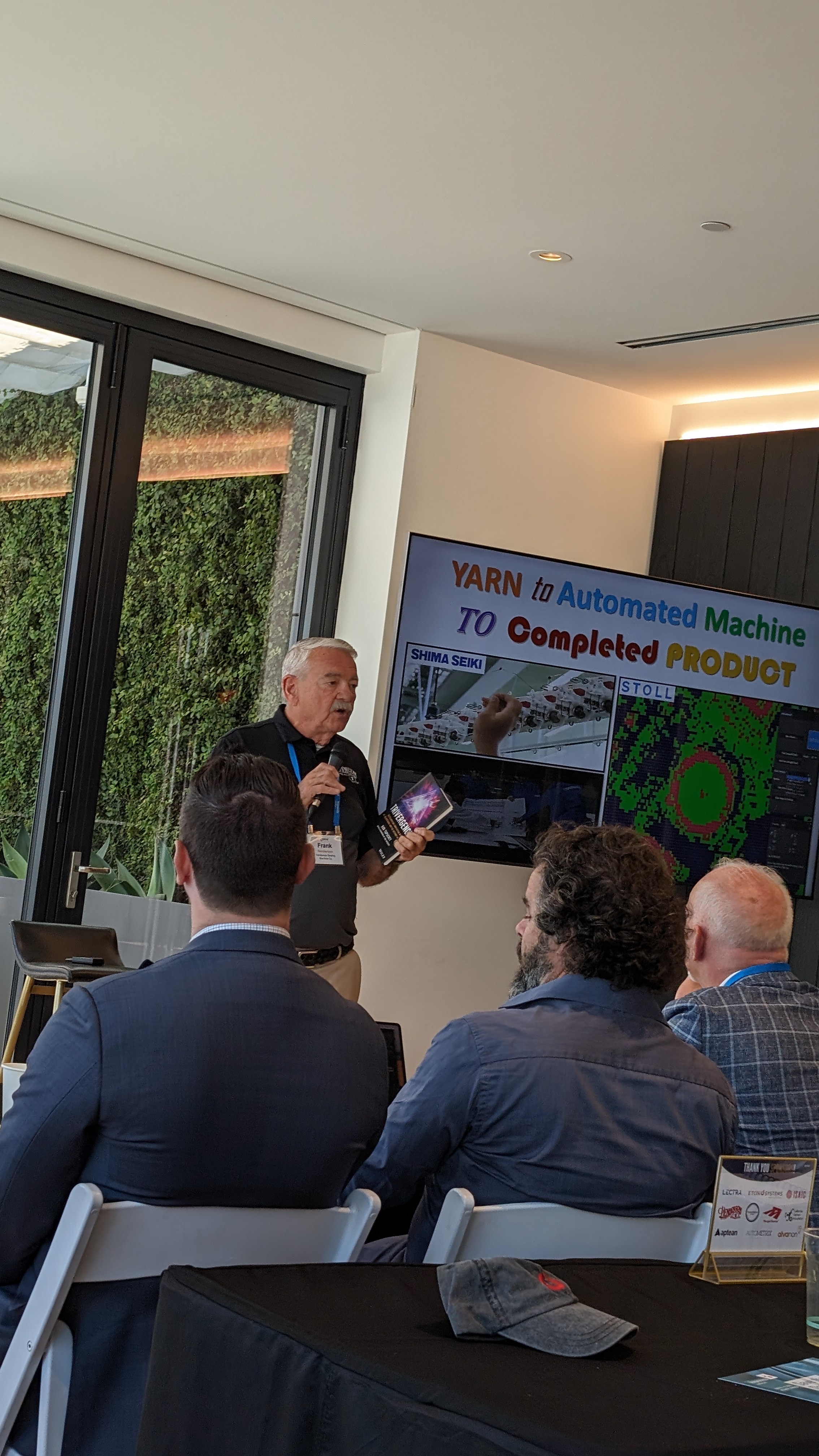
Next, the topic shifted to Industry Evolution - Automation and Advanced Manufacturing with Frank Henderson (Henderson Sewing Machine Company) and SK Gupta, Ph.D (University of Southern California School of Engineering; Director, USC Center for Advanced Manufacturing). They acknowledged that the US workforce has not been well invested in, but that those working have vast knowledge and are mostly welcoming to changes that would help make their jobs easier, faster, more efficient. Many factories that operate today have operated the same way for decades, no automation, even invoicing on paper or not utilizing email. That’s insane to think about. Henderson was quick to ask, “How many of you drive a car from 1960? But, you operate a sewing machine from 30-40 years ago? That’s dumb shit.”
Audience members got involved with some great insights. Jen Guarino (ISAIC) raised the point that the industry has been “built on the backs of women”, and sewing is still an underrated skill set. She suggested making women the “masters of the tech”, as well as stating, “If you want young people, it can’t be the bare minimum. We need to raise the bar higher.”
Guadalupe Tlatenchi (GTLA) chimed in, “In order to attract new people, [we must] make a more attractive industry.”
To the point where people may be hesitant to adopt technology, Michael McDonald summed it up well: “People matter. Robots are not taking anyone’s job. Industry can be so much better with things that exist right now. It starts with the people.”
Technology is America’s best bet when it comes to competing with foreign markets (specifically Asia), but also a way to make worker’s lives better and easier. Industry needs to work with its people, but utilize people’s skills differently. A single operator and a mechanic can do the jobs of many when paired with robotics and automation. Dr. Gupta reminds us that human programmers are needed to program machines, and there are many digital opportunities for growth. Cameras become our eyes, robots become our arms. The costs for these technologies are coming down as AI is becoming more sophisticated. The issue is getting the right tech into the right hands.
I asked, What is the resistance against implementation? Frank Henderson answered by sharing that for most factories to invest, they need more volume of production domestically. Very few brands in the US are vertically integrated, and don’t know much about manufacturing, and they don’t share the costs with their suppliers.
Volume is needed in order to sustain the investment of money, training, and resources. And the reason the US is so far behind other countries is because there is not widespread implementation of this technology - which finds us in an interesting place, a Catch-22.
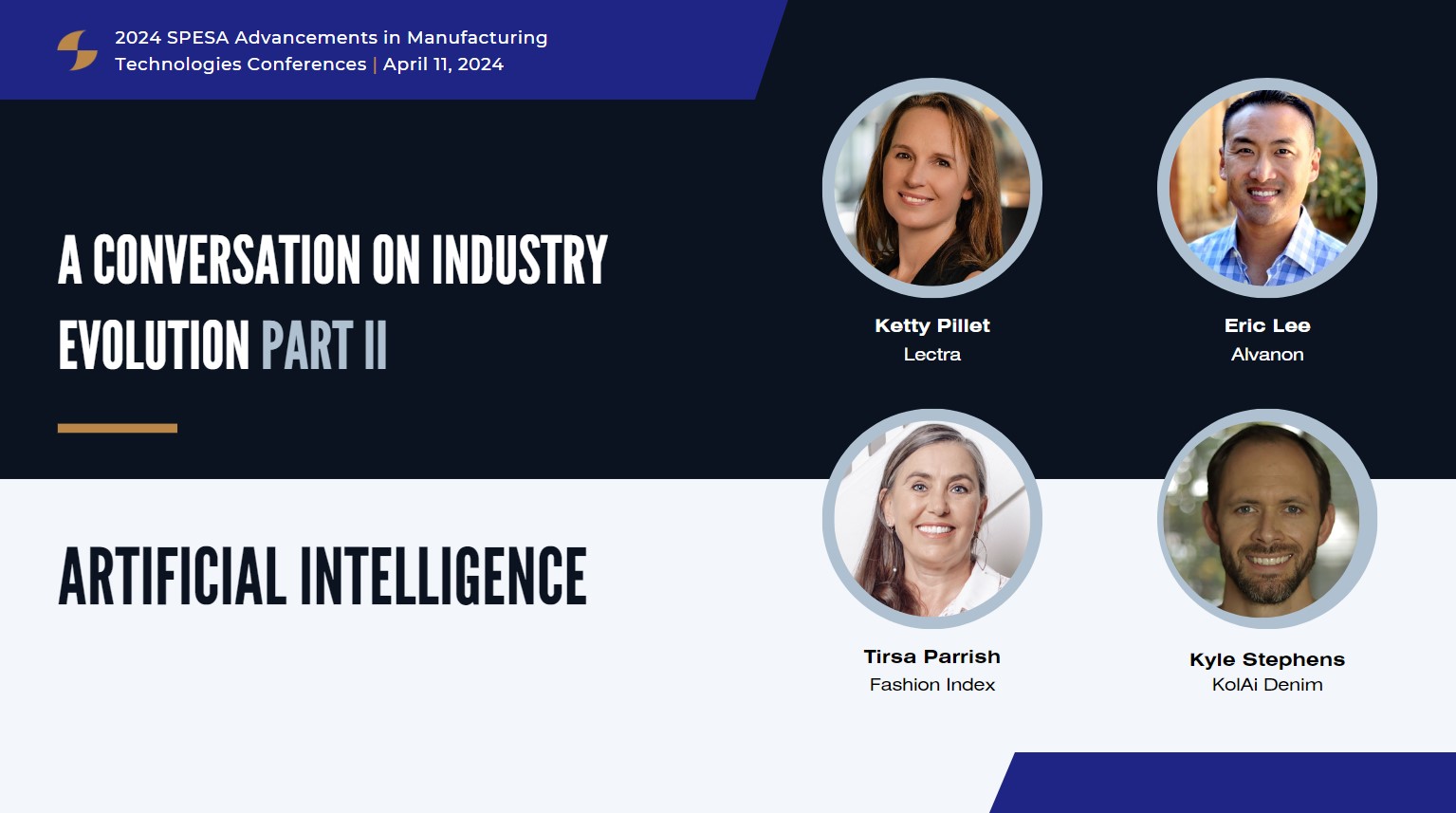
Artificial Intelligence (AI) and Industry Evolution was the next topic, which is hugely broad, and a wildly popular buzzword we are now hearing everywhere. Michael McDonald opened up the talk by first asking the audience, how they are utilizing AI in their companies? Many acknowledged the use of ChatGPT as a starting point. ISAIC is using AI for QC inspections, as well as transcribing video or audio into written format in multiple languages. Aptean is integrating Amazon’s Alexa to share through its Shop Floor tablets what is happening on the production floor, when maintenance is needed, or when to move labor or job functions around to improve efficiency.
Panelist Ketty Pillet (LECTRA) talked about how AI relies on good data, their Retviews program allows for brands to utilize sales data from across competitors to see what styles, colors, sizes, etc are selling with competitors so that they can make adjustments to their own inventories, or introduce short runs on new designs.
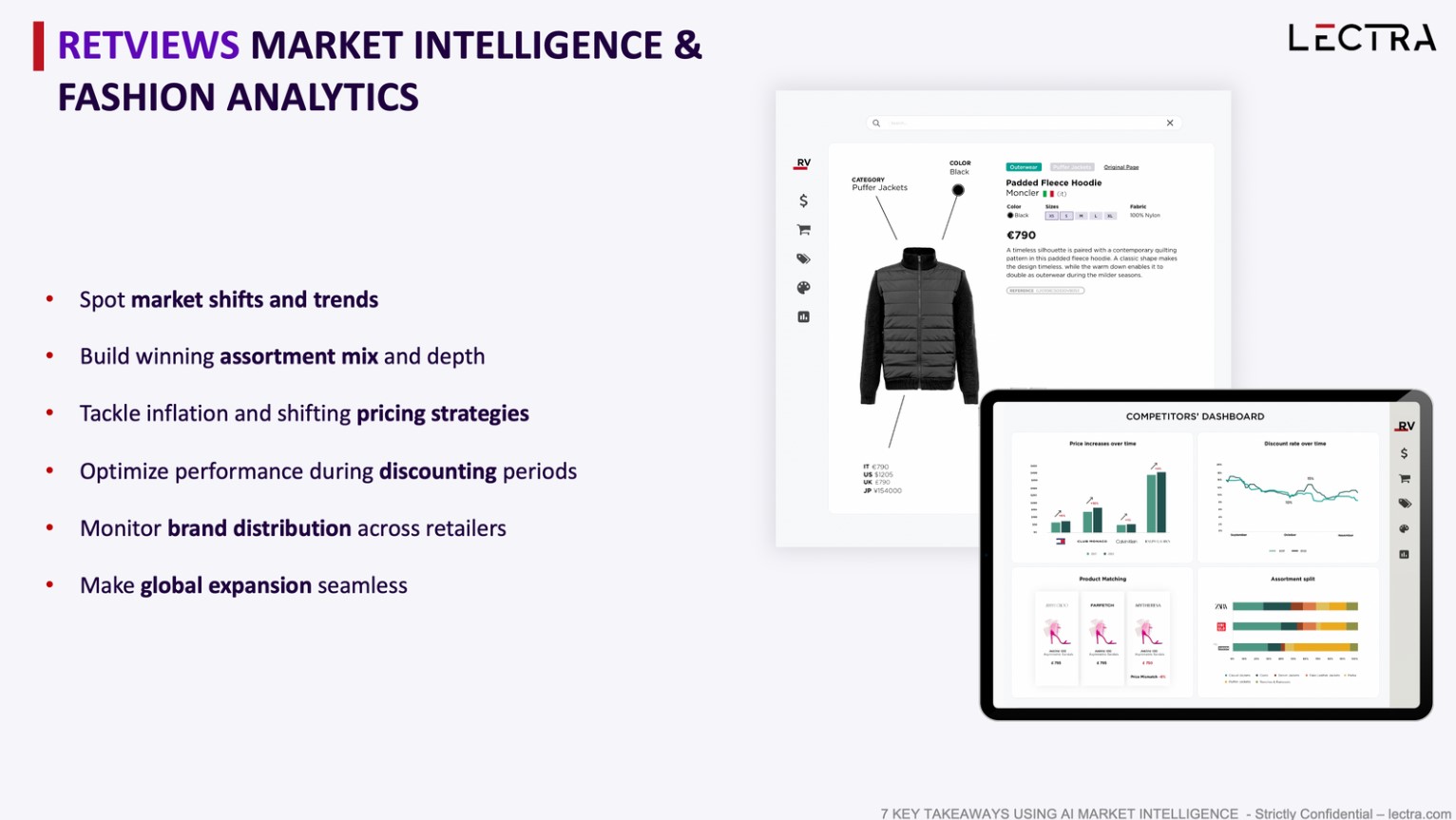
Kyle Stephens (KolAi Denim) took his experience at Kontoor Brands which manufactures Wrangler and Lee brands, along with an interest in technology to train machines to create laser patterns for denim whiskering. What once took a person a painstaking 8 hours to complete, now takes about 20 seconds, and a human is still involved to clean up and finalize the design file.
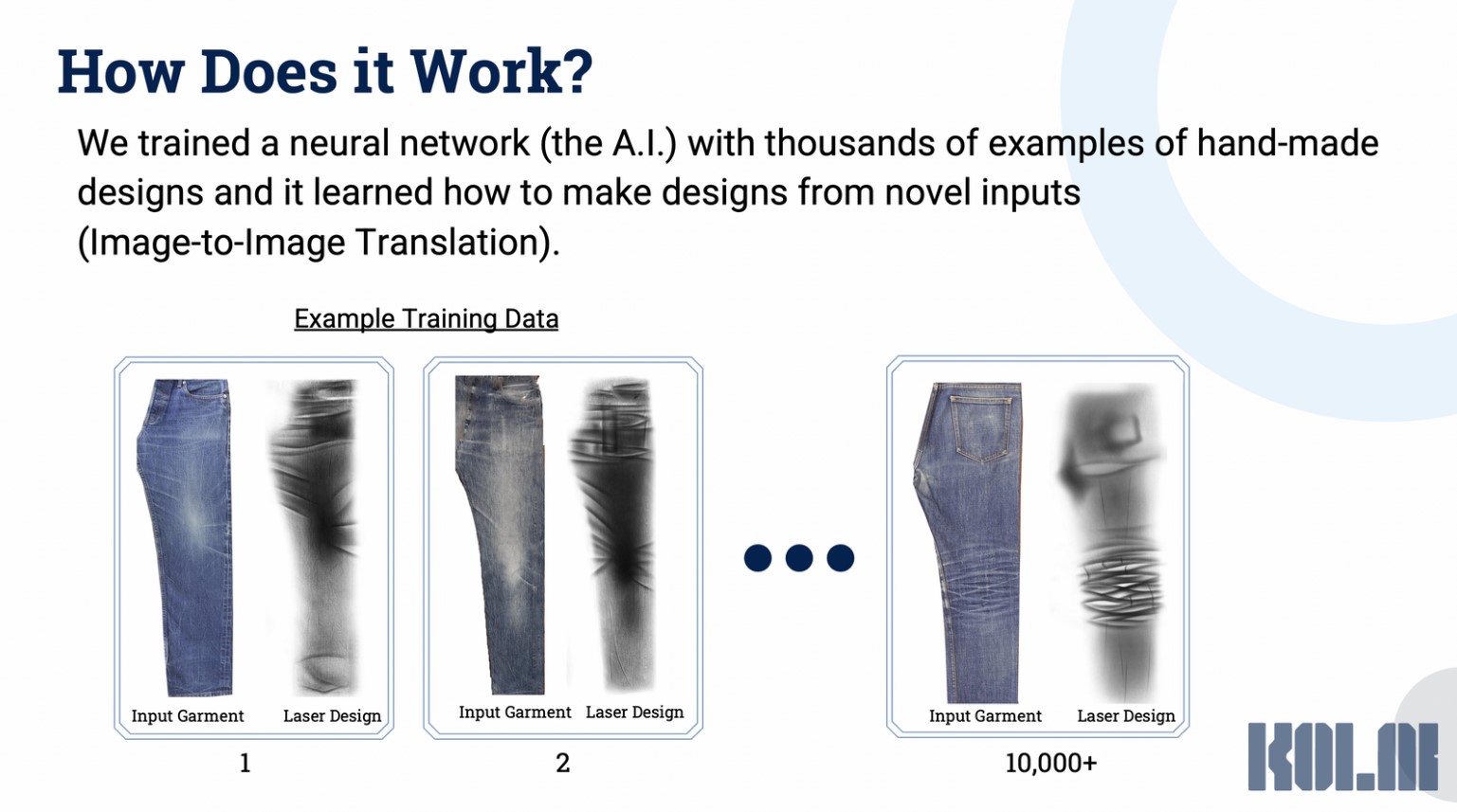
Eric Lee (Alvanon) discussed the adoption of 3D prototypes or simulations from pattern files, and how far digital twin body forms and scans have come in the last 3-5 years alone. He says this not only helps on the design and development side by speeding up the process and reducing number of sample iterations, but also on the retail side, where consumers can conduct more accurate virtual try-on’s, thus reducing the amount of e-commerce returns due to needing to purchase multiple sizes to try on, or not finding a fit at all.
By the end of the discussion which spanned intellectual property concerns, to evaluating the integrity and accuracy of AI’s sources. It’s important to remember that the output is only as good as the input. Ketty Pillet suggested that those who were a little apprehensive to try it out, to try to “think of AI as a smart child,” it would still need to be taught by a good teacher (programmer). Michael McDonald suggested those interested in trying out the tech should contact local universities to find talent, figure out ways to tackle problems with a fresh perspective.
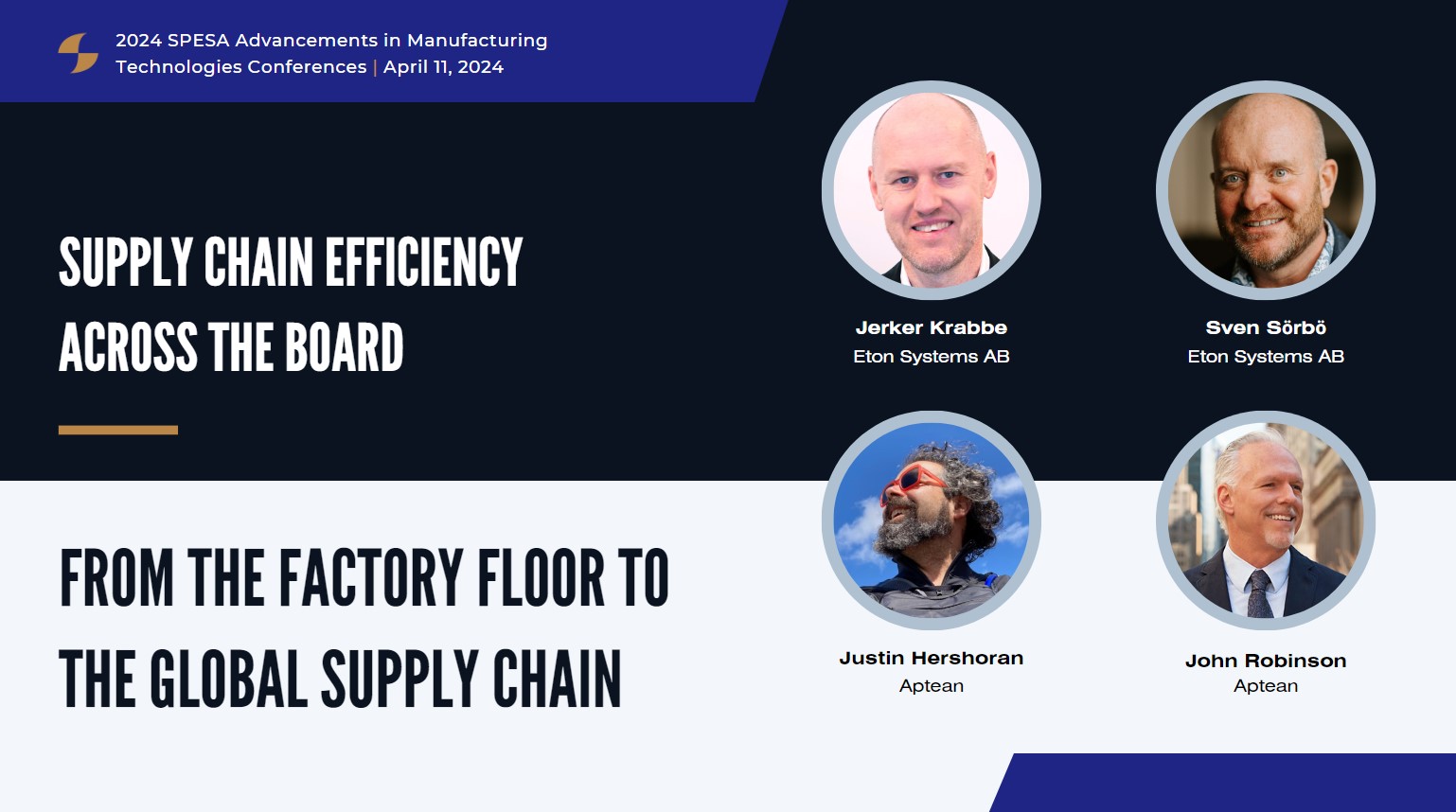
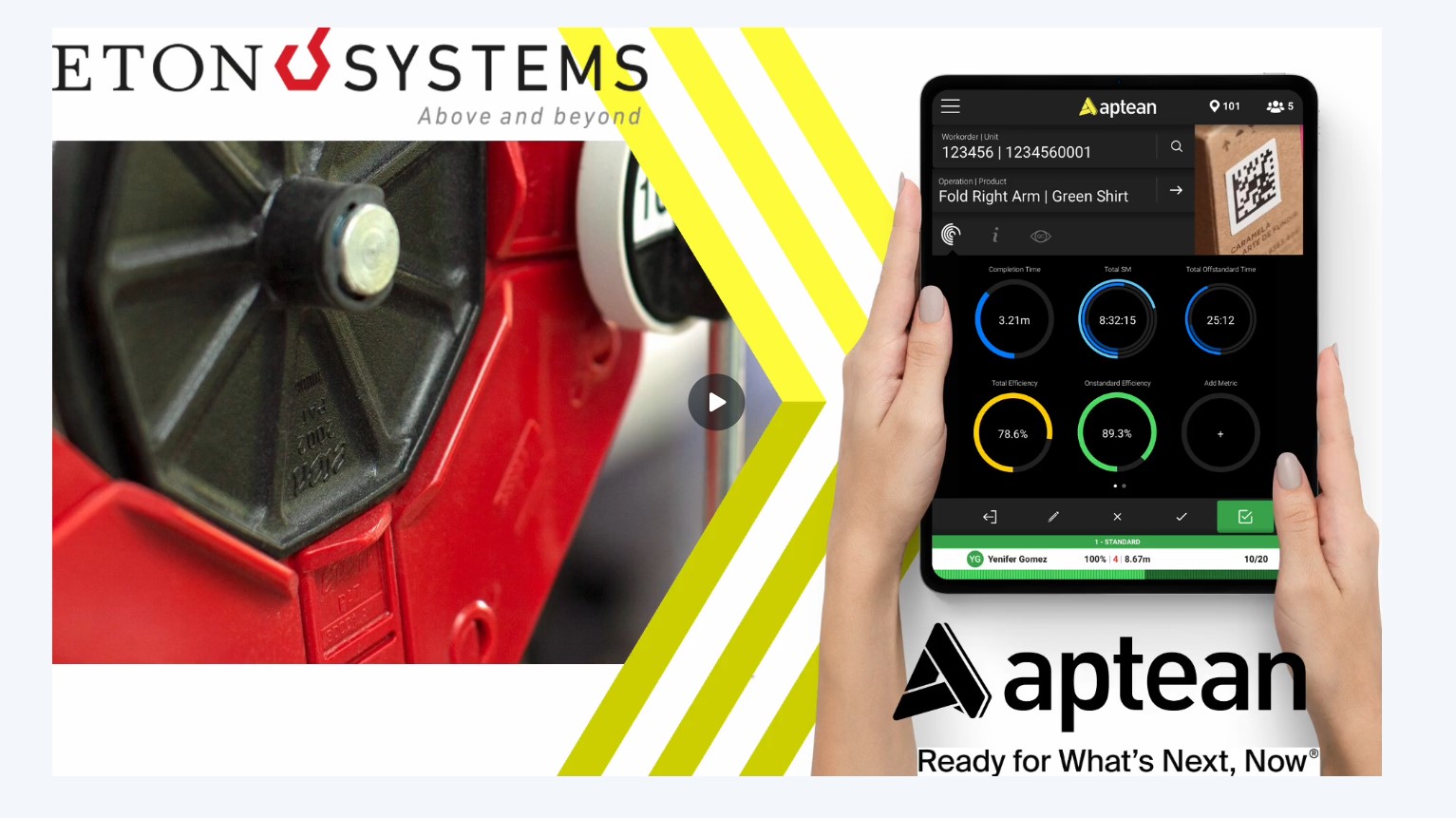
Supply Chain Efficiency was up next - with representatives from ETON Systems and Aptean Apparel. The talk focused on how to create better supply chains that are more connected and sustainable for the long-term. Although very tech focused, a lot of the consideration was put on the worker wellbeing, tying back into earlier topics. It isn’t always factory management against the worker, but about building trust, transparency in the systems, and helping operators train and upskill in order to make more money. Justin Hershoran shared how operators can “see their numbers go up or down,” which builds “trust and motivation.”
The Sustainability in Garment Manufacturing panel discussed navigating overproduction issues and waste management, through various means. Morgan Technica, which makes cutting systems, focuses on reducing waste material, and energy consumption.
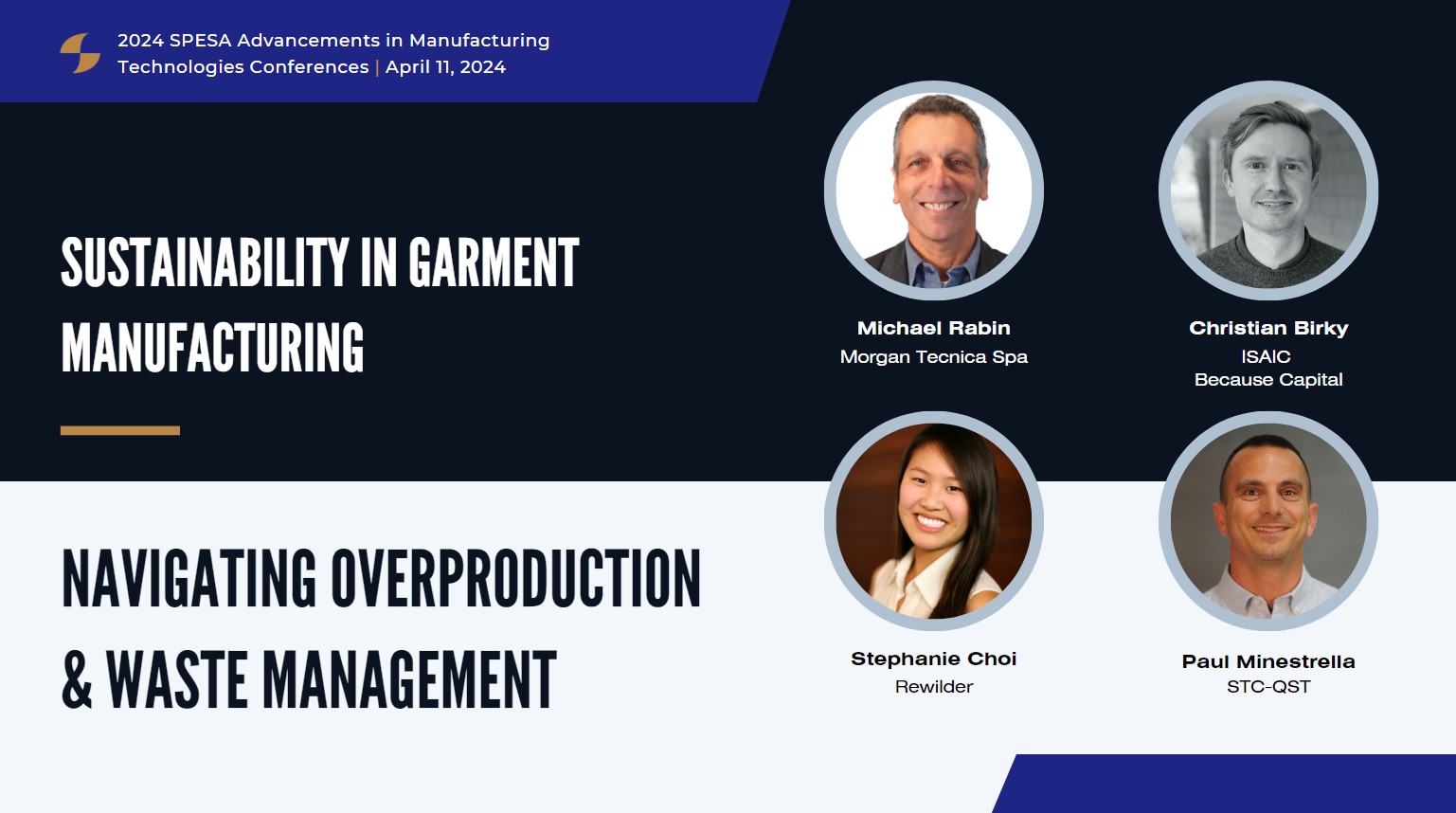
A topic that continues to be widely discussed in the industry is that of eco-friendly products and what initiatives companies can implement to become more environmentally conscious. Rewilder works with brands to divert scrap material and create new products from what would otherwise be waste. This was a really interesting company to learn about, given many of our Columbia students interest in upcycling and sustainability practices. Many smaller scale projects have focused on these objectives, but it was really cool to see this done on a larger scale and with bigger brands including Michael Stars, Hollywood Bowl, and others.
QST is one of the largest component suppliers in the garment industry, offering pocketing, lining, fusible, elastic, and other components that make up the “guts” or inside of the garment. Within these product categories, they’ve created eco-friendly items that are Oeko-Tex certified, use Repreve or Better Cotton Initiative fibers, or utilize “Low-Water” finishes to appeal to brands looking to market their products as eco-friendly.
The problem is that while many brands (and consumers) are demanding these sustainable materials, they are not willing to invest in the higher prices that come with it. Similarly, the Made-In-America initiative has been frequently discussed for many years. With this label means higher prices on products, which can be attributed to fair wages, higher-cost materials, and more expensive overhead. Time and again though, consumers state when surveyed that they will pay more for Made-In-America products, but statistics show the reality is that most don’t actually purchase the more expensive option.
Finally, Because Capital is a partner of ISAIC, and seeks to find intersections between sustainability and profitability. Christian Birky points out that this is “not a technology problem, it’s a business model problem.” The most profitable brands in the US don’t have any manufacturing footprint in the US, which further contributes to why American sewn products factories are so far behind the rest of the world when it comes to manufacturing technology. They desperately need financing solutions in order for them to implement and compete with the rest of the world.
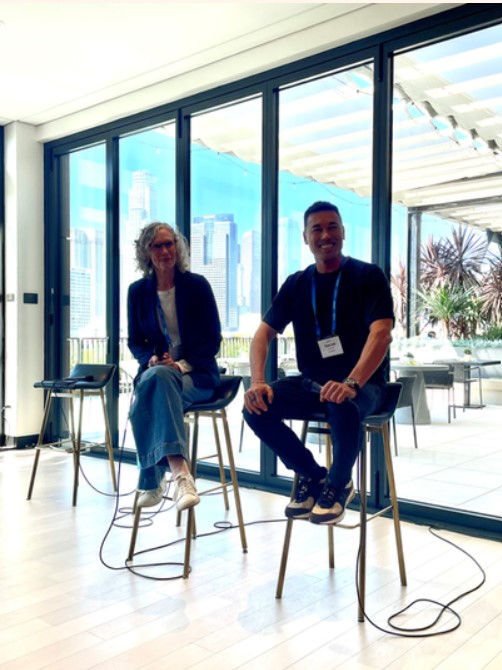
The next talk is a case study presentation of the partnership between Variant 3D and ISAIC in Detroit. This was really cool to hear about because I was first introduced to Variant as a speaker at the 2022 SPESA Conference. In this talk, they described how they worked on a pilot program testing Variant’s 3D modeling software, and test marketing it with the auto industry. As a non-profit organization, ISAIC is able to take out a lot of the risk associated with this type of development, prove that it works well, before it is later sold commercially. For their efforts, they become the training arm for a company such as Variant 3D. Additionally, ISAIC runs other training programs including a sewing operator program, with the goal of upskilling workers to sew in factories, or to open their own micro factories.
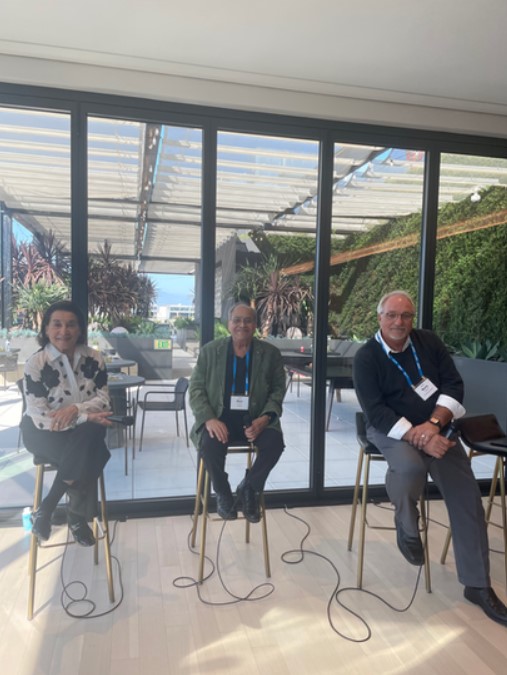
The last panel focused on the future of the industry in LA specifically, however I think that the points raised apply outside of the West Coast as well. Isle Metchek (California Fashion Association) began by discussing the role of the next generation. Design departments in colleges and universities are overrun - it’s a popular major but many other roles need to be filled to support this.
One goal for both current and incoming workers of garment manufacturing is getting operators excited to be around technology and innovative products and making sewing manufacturing a “cool” place to work. Traditionally, the job of a professional sewing operator has been seen as less than ideal. Although it is now illegal in California, piece-rate is still being widely used to pay operators. Working conditions are not always up-to-code or as safe as they should be. Those in the industry want to change this negative perception and “rewire” what it looks like to work in garment manufacturing. To achieve this, fair, living wages need to be offered, and the work environment for operators needs to be inviting.
We got to see this first hand during the tours the following day, where we visited US Standard Apparel (USSA) and the Tukatech Innovation Center. Additionally, I arranged a separate tour before the conference at Lefty Production, which offers product development, sourcing and production services. At USSA, the facility was welcoming, modern, and incredibly clean. It housed a showroom for guests, and a beautiful full kitchen space and break area for staff. It is a great example of what manufacturing can and should look like in the US. The technology integration, and the clear focus on worker well-being shows why this business model is a success. It's a relatively rare example of a vertically integrated brand which offers both retail, wholesale, and custom production options.
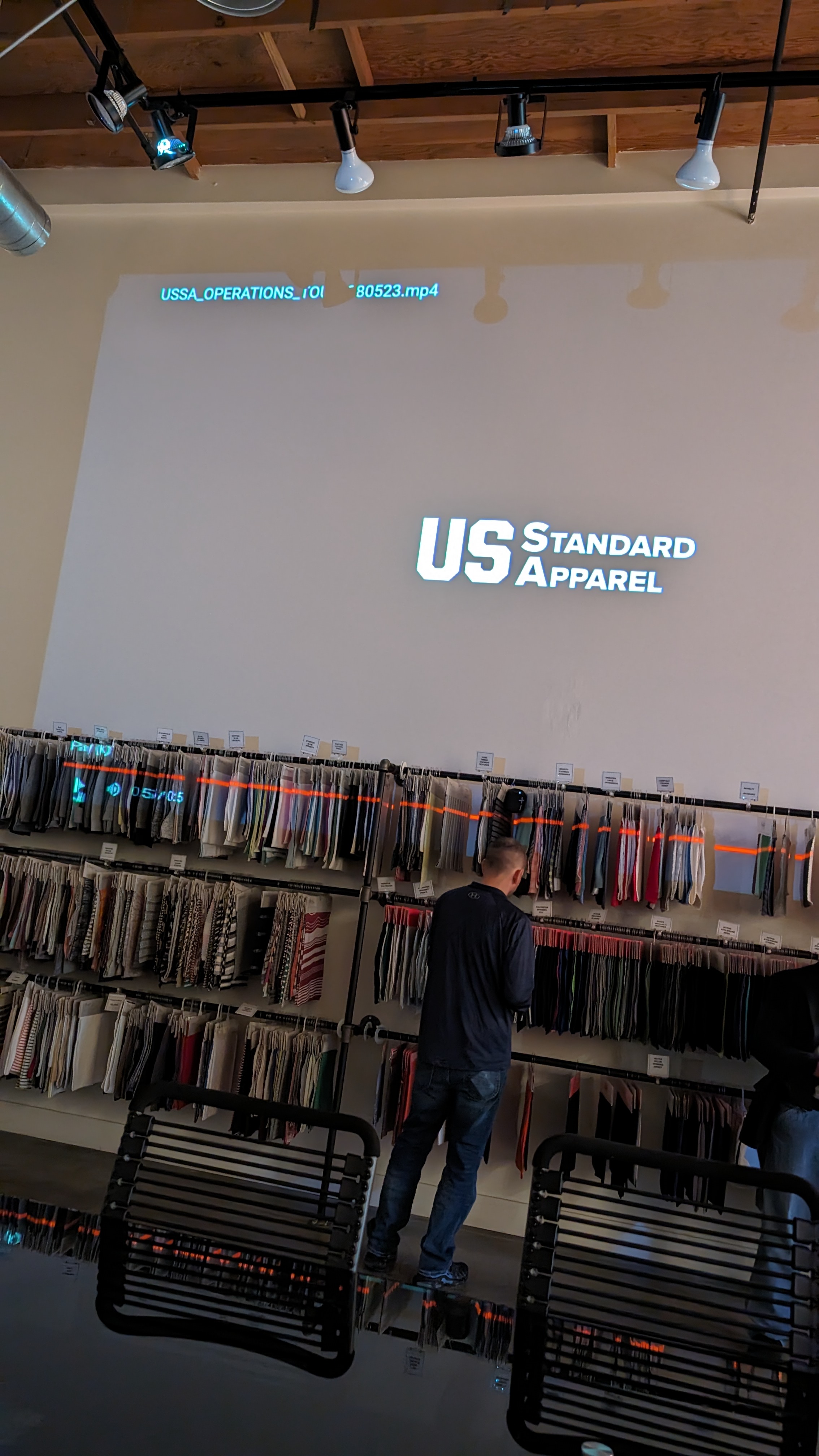
Tour - USSA Factory
The Tukatech Innovation center focuses on providing services on an as-needed basis for designers, brands, and small batch factories who may not have space or funds to house all these things in house, particularly for things they don’t need every day. Tukatech has just over 70 centers worldwide, each offering services which cater to its locality. In LA, visitors have access to software including 2D and 3D pattern CAD systems, supported by a lab upstairs which tests the physics of materials to be incorporated into a design, making a digital material which is comparable to the behaviors and characteristics of the real thing. A wide format printer allows for digital print design to come to life through sublimation prints, and a full size cutting machine and many industrial sewing machines makes a fully equipped sample room of a full factory accessible to a smaller brand, or allows for an existing brand to utilize services and equipment as needed, vs making a full investment in something they use occasionally. Users can “DIY” aspects on their own, or tap into the expertise of the TUKAcenter to support them. A sewing cell featuring a conveyor system shows how a micro factory can operate successfully with big volume in a small footprint.
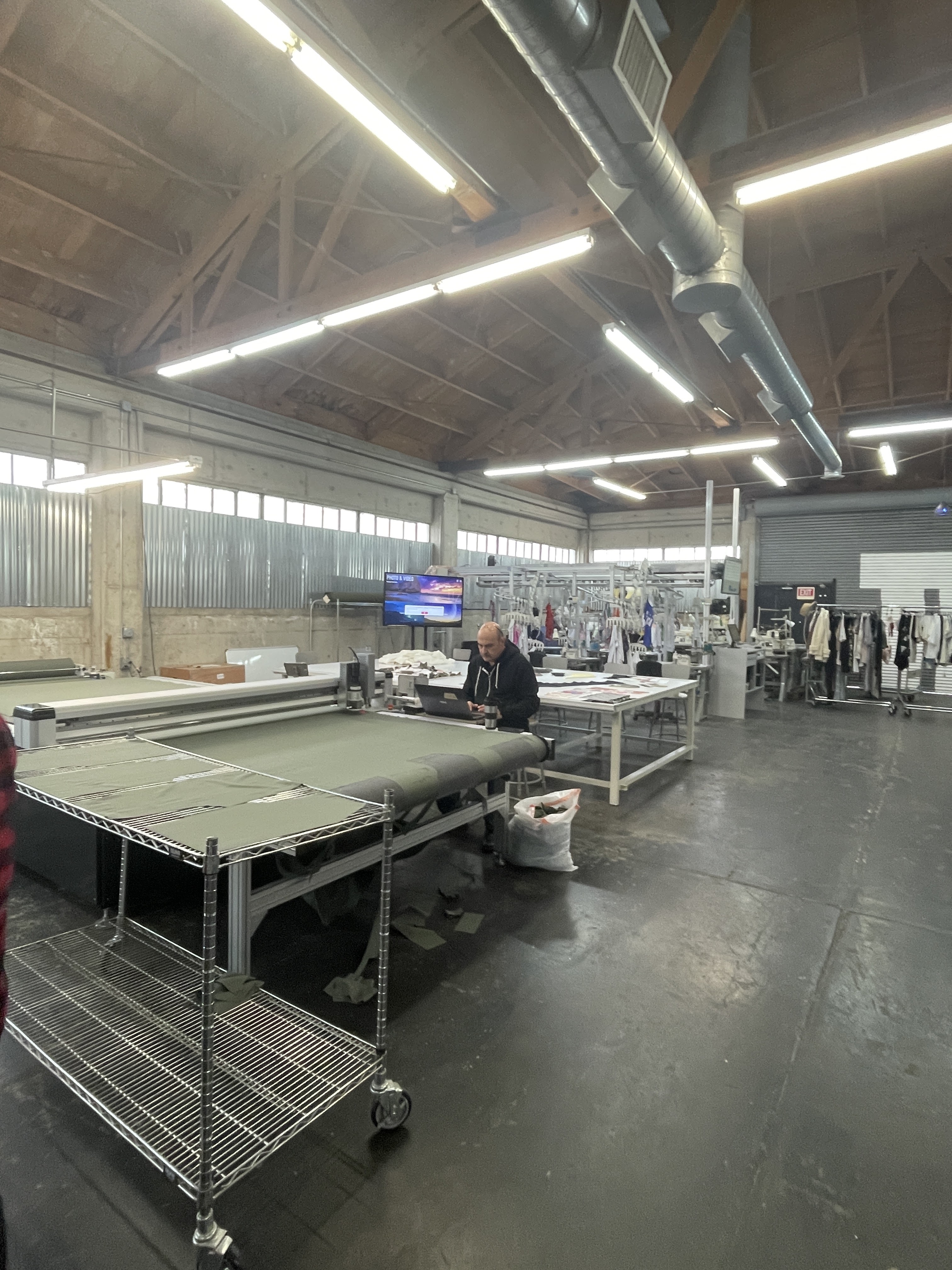
Tour - TUKATECH Innovation Center
Something which was brought up in several talks was the topic of education and four-year degrees. The tide seems to be shifting from companies wanting their employees to have a traditional Bachelor's degree, to being more accepting of junior colleges and associate’s degrees. The main reason is that the garment industry needs people who want to make the product, not just focus on the creative and design side of the business.
While sewing operator training absolutely has a place in community colleges, I do think there is a huge opportunity for schools like Columbia to remain competitive in the industry by focusing on technology. Our Fashion Studies department has done a great job of integrating 3D design and pattern making, but we could go further with some specializations or even introducing certificate programs in those areas. I think it would be great to explore further AI-assisted design and its role in the educational and professional practice of fashion design. There are many opportunities to grow these or integrate them into existing curriculum so that students can be better prepared for this ever-evolving world.
In all, this was a great conference and I’m incredibly thankful for this opportunity to have attended on behalf of Columbia College Chicago. I learned so much and was exposed to new ideas that I have only really read about. I think with technology especially, it can be difficult to quickly implement new curriculum and educational resources as the technology is being updated as we do. However, we need to make sure it is a priority for our faculty to stay on top of it so that we can provide the best education possible for our students.
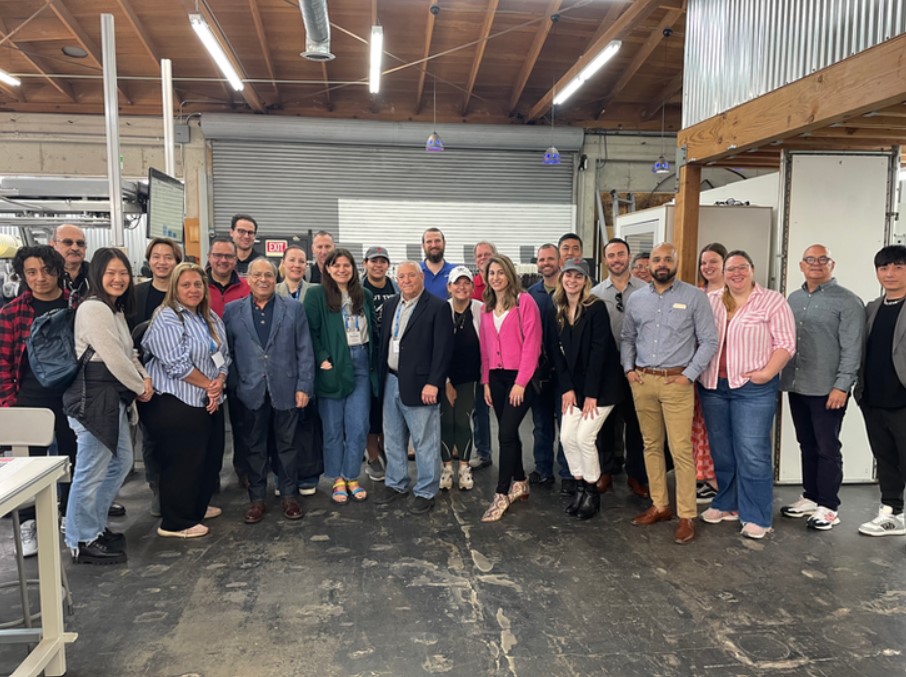
SPESA Tour - TUKATECH Innovation Center